Ceramic raw materials are usually classified according to their functions in ceramic manufacture as well as their basic properties. It generally divides the ceramic raw materials in two basic groups that are the plastic and non-plastic raw materials. Further detail division depends on the material composition [1].
Plastic ceramic raw materials involve any clay material that when mixed with water reveals the property called plasticity. Plasticity may be defined as a property which allows the deformation of the clay when an external force is removed [2]. The large group of non-plastic ceramic raw materials include minerals, rocks and artificial chemicals that when mixed with water is not plastic. A part of the non-plastic ceramic raw materials acts as a filler, reducing high plasticity or shrinkage of the body when drying or firing. On the other hand, other non-plastic raw materials are used for sintering, fluxing and melting or to increase the refractoriness [1].
Plastic raw materials include kaolin, clay and bentonite while non-plastic raw materials are feldspar, quartz, limestone, dolomite, magnesite, calcium phosphate and talc. The classic or "triaxial" ceramic body consists of three major components: clay, quartz which is a non-plastic material and feldspar, that acts as a flux providing the glassy phase [3]. Typical raw materials normally used in a ceramic tile are clay, feldspar, pottery stone, silica sand and talc.
Clay
Generally, the most important component of a ceramic tile body is clay. Clay is a term for naturally occurring mineral aggregates consisting mainly of the hydrous silicate of alumina. There is considerable variation in the clay's mineral content and degree of purity.Clay serves various functions such as a binder, a suspension aid and an inexpensive source of alumina and silica. Figure 1 shows a clay mine in operation.
From a geologist's viewpoint, kaolin is produced from feldspar and on feldspar crystals under the influence of weathering or acidic water[4]. The term weathering means wearing down of all exposed masses of rock tending to reduce the land surface to sea level by different agencies such as water, wind or glacial. It is either a mechanical or physical process. Water in the form of rain or waves continuously wearing down the surface of rocks is a mechanical process. Wind moving at a high velocity can be destructive as well. The formation of clay is a chemical process that is assisted by mechanical breakdown and the separation of fine particles from coarse grains [5].
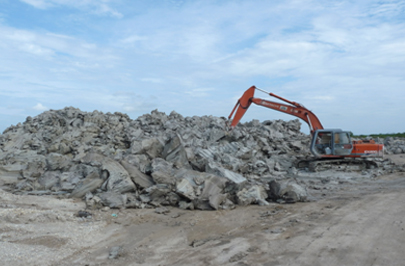
Clays were formed by alteration, through aging and weathering of rocks such as granite, feldspar, mica and quartz. At the origin, they are known as residual or primary clays. The clays were formed at the site of the parent rock and were not transported by any of the various agencies such as wind and water. Primary clays for eg. china clays are usually found in irregular pockets with unaltered rocks remaining. These deposits are coarse grained and non-plastic as the clay was not transported by water [6,7]. Therefore, there was no selective sorting of various particle sizes. Primary clays are normally uncontaminated by non-clay minerals as most of the primary clays originated from pure feldspar. Most kaolins are primary clays [6]. The fired colour of the china clay is white as it has a high degree of purity. Therefore, it is suitable for manufacturing china and porcelain. In addition, it is refractory due to its low impurity content. Figure 2 shows a micrograph of the kaolinitic stack using the polarizing microscope (transmitted light).
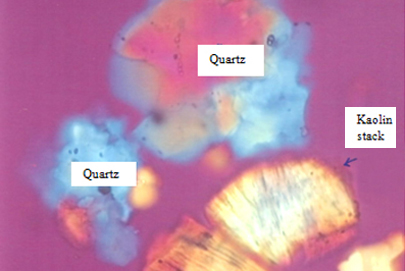
If the clays are transported by wind or water from their original point of formation, they are known as sedimentary or secondary clays [8,9]. The action of the water tends to grind up the clay into a much smaller particle size. Sedimentary clays for eg. ball clays depend on their fine particle size for remaining in suspension whilst they are being transported. This process of sedimentation separates the coarse from the fine and only the very fine particles will be carried to the final deposit. The sedimentary clays are likely to be contaminated with impurities or accessory minerals that are picked up along the way such as muscovite, biotite, quartz, iron oxide, rutile and garnet [6]. Transported clays are usually made up of clay from various sources. Sediments from numerous sites are likely to be mixed together with the presence of carbonaceous matter. Secondary clays are therefore fine-grained and plastic. Glacial clays and aeolin or wind deposited clays are also considered secondary clays. The fired colour is normally more buff than china clay that is usually white. The presence of organic and other impurities as they were re-deposited in low lying swampy areas may be the root cause of the darker fired colour. The ball clays are mainly kaolinite but they are much finer than china clay and the impurities present are also very fine as well.
The sources of clay-forming minerals are aluminouse rocks, particularly those containing feldspar. The ore is regarded as kaolin formers, especially orthoclase, KAlSi3O8 and albite NaAlSi3O8. Feldspars are usually crystallized out of the solidifying magma together with other minerals [4].
Kaolinisation of feldspar may be shown by the following, chemical reaction:
Feldspar + Water + Carbon dioxide ------> kaolinite + quartz + potassium carbonate
KAlSi3O8 + 2H2O + CO2 ------> Al2Si2O5(OH)4 + 4 SiO2 + K2CO3
Clay is the fundamental raw material for all ceramic bodies. The functions of the clays in the ceramic tile are as follows:
- produces a light colouring during firing
- gives plasticity and binding characteristics to the mass
- enhances mechanical characteristic in the fired tiles
- produces good rheological flow properties
- gives a good density level during firing due to the individual characteristic of the clays.
Feldspar
Feldspar is an important and common fluxing material for ceramic bodies as well as glazes and one of the three essential raw materials for the triaxial body. Feldspar provides the glassy phase for the ceramic bodies and they are added to decrease the firing temperature and thus to reduce cost [3]. Feldspars are found in pegmatite rocks usually of the granite type which can be considered as a mixture of feldspar minerals together with quartz and mica [9].
The feldspar mining operation uses the conventional open-mining system whereby the overburden is removed by bulldozer or backhoes followed by drilling and blasting. Crushing is then carried out with a jaw or cone crusher after which screening through different apertures are done such as 5mm or according to market requirement. Magnetic separators are also used to remove contaminants (for eg. iron). Figure 3 shows the sampling procedure at a mine.

There are three types of feldspar minerals namely Na-Feldspar (Please see Figure 4) or albite, the K-Feldspar or orthoclase and Ca-feldspar or anorthite. Pure feldspar does not occur in nature but are intermediate in composition. Therefore sodium feldspar also contains orthoclase and anorthite. Accessory minerals are present as well such as quartz, iron compound and magnesia [10].
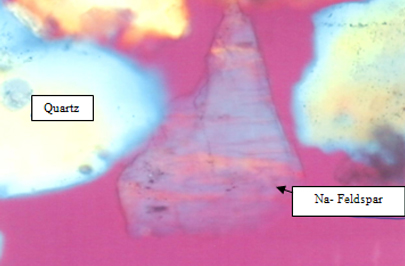
In the ceramic tile body especially the porcelain tile, feldspars play an important role in achieving the vitreous nature of the body and the high mechanical resistance of the product at the end of the firing stage. Besides acting as a flux, feldspars also facilitate drying and release of gas during firing like other non-plastics.
Silica
Silica is the most abundant oxide on the earth's crust [11]. A large amount of silica occurs as free silica that is mostly in the form of quartz although most of it is combined with other elements in the silicate minerals.
There are 3 types of silica found in nature that are rock, granular and powdered [3].
- Rock type - This type is also known as quartz stone. Due to its impurities content, this type of silica is not commonly used in the ceramic industry.
- Granular Type - This form of silica is known as silica sand and is the most commonly found. This type of silica is widely used in ceramics because it is rather pure even without beneficiation.
- c) Powder Type – This amorphous type of silica is known as diatomaceous earth and contains a considerable amount of impurities. The usage is not in ceramics but mainly in thermal insulation.
Silica exists in a great variety of forms. The three principal crystalline forms are quartz, tridymite and cristobalite [3,12].
Quartz as compared to the other raw materials in the ceramic bodies is relatively cheap. Silica sand or flint is used in the body as a source of silica. Addition of silica sand decreases its unfired strength and plasticity but assist to facilitate escape of gases during drying and firing. It also reduces drying shrinkage and increases the whiteness of the fired body [10].
The other constituents besides the basic clay, feldspar and silica sand includes a number of minerals that are used for modifications they create within the characteristics of the bodies themselves. The most important component in this group is talc which is used to increase the fusibility. Wollastonite, dolomite, magnesite, nepheline syenite are other minerals that are used to assist the vitrification process of the body.
Talc
Talc has the chemical composition 3MgO.4SiO2.H2O and is used in small quantities (2-6%) in the vitrified tile body composition to enhance the fluxing action of feldspathic materials. Talc is formed by the interaction of water with magnesium salts on primary rocks. Use of small amounts of talc with feldspathic fluxes can lead to higher modulus of rupture in the fired product and improved whiteness level [10].
- Konta, J. "Properties of Ceramic Raw Materials" Ceramic Monographs- Handbook of Ceramics. Verlag Schimd GmbH Freiburg i. Brg, pp.1-21 (1980)
- Lawrence, W.G. "Ceramic Science for the Potter" First Edition Chilton Book Company, pp.82-117 (1972)
- Lee, W.P. "Ceramics" Reinhold Publishing Company, pp.7-35 (January 1961)
- Salmang, H. "Ceramics Physical and Chemical Fundamentals" Butterworth and Company, pp.20-27 (1961)
- Clews, F.H. "Heavy Clay Technology" Academic Press, pp.1-16 (1969)
- Rhodes, D. "Clay and Glazes for the Potter" Chilton Book Company, pp.1-21 (1972)
- Jackson, G. "Introduction to Whitewares" Maclaren and Sons, (1969)
- Ryan, W. "Properties of Ceramic Raw Materials" Pergamon Press, pp. 21-36, pp. 43-82 (1978)
- Sen, S. "Ceramic Whitewares – Their technologies and Applications" Oxford and IBH Publishing Co. Pvt. Ltd., pp.
11-43 (1992) - Ryan, W. "The Manufacture of Wall and Floor Tiles" Ceramic Research Company, Malaysia, pp. 52-75 pp. 99-147, pp. 185-200 (1999)
- Worrall, W.E. "Clays and Ceramic Raw Materials" Second Edition Elsevier Applied Science Publishers Ltd, pp.30-44, pp.127-139 (1986)
- Rado, P "An introduction to the technology of Pottery" Second Edition Pergamon Press, pp.1-34 (1988)