The production process of ceramic tiles is illustrated as in Figure 1
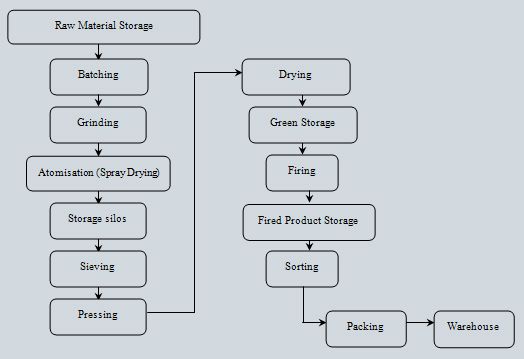
Figure 1: Flow chart of Production Process of Vitrified Tile. After [1] Biffi pg.28
The preparation of the body begins with proportioning or batching of the various raw materials in the correct amounts. The mixing of the body from individual components follows the coarse-crushing of the raw materials and is carried out according to the body formulation. Nowadays, coarse-crushing of the materials is often performed by the raw materials suppliers [2].
The batching or proportioning may be done by volume or by mass. However, proportioning by mass is far more accurate than that by volume and is thus preferred. Automatic raw material weighing and feeding has enabled better control of the mixture of raw materials, reducing possible variations that could lead to a change in body properties [3].
The grinding of solid raw materials involves a whole series of operations aimed at reducing the size of materials. The purpose of grinding is to obtain smaller particles out of coarser size ones. Besides that, it also increases reactivity of materials (especially feldspar) so that firing is efficient as well as to give a size distribution of materials such that they can pack to give a high packing density [4]. There are essentially two methods of grinding namely the wet and dry grinding method. In both cases, the fineness of the materials needs to be brought down to eliminate dangerous impurities that can cause spots or faults [2].
For the wet grinding method, the different raw materials such as clay, flux (feldspar) and filler (normally sand) that make up the body composition are stored in separate bays. The raw materials are weighed proportionally according to the formulation and charged into ball mills (Figure 2) together with suitable amounts of water and deflocculant to ease dispersion. One of the purposes of milling is to obtain a high compaction in the body powder, by producing a range of coarse, medium and fine particles in the particle size distribution of the ball mill slip [4].
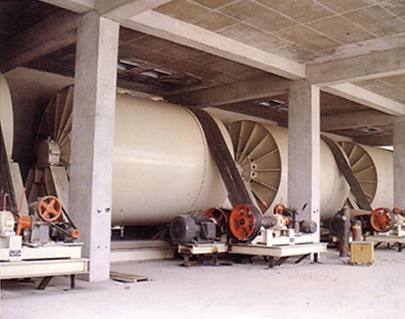
In the wet batch milling, the mill is charged, milled and then discharged followed by filling with a new charge for milling. Once the slip has achieved its desired particle size, it is discharged into the underground storage tank and aged for 24 hours. The second grinding method is dry grinding. There are several types of mills which grind raw materials with moisture contents of up to 8 or 10% down to 100% pass through a screen of <63µm. A version called "Novorotor" from Hazemag was applied in Central Europe. Hammers hanging on hammer bolts served as grinding tools. The milled material is discharged pneumatically or mechanically [2,5].
From the technological point of view, the same degree fineness of grinding is not possible with dry grinding as can be achieved with wet grinding. The wet grinding method is at present the most commonly utilised method in the manufacture of porcelain stoneware tiles. By the wet grinding method, the granulated powder obtained from the spray drying process is more suitable for properly filling the presses due to its optimum shape and particle size distribution. Contaminants that may be present are eliminated with sieving the slip obtained by wet grinding [4].
For ceramic tiles, spray drying is the process that converts the body slip obtained from the mill to a granulate with a size distribution and moisture content suitable for pressing. The body slip is atomised under high pressure, and water is evaporated from the fine droplets using a flow of heated air [6].
Figure 3 shows the schematic construction of a spray drier. A volumetric pump sends the slip to a set of lances placed inside the dryer. At the lances' extremities, the slip is atomized into fine particles by nozzles and then is sprayed toward the top of the drying chamber against concurrent descending hot air that rapidly evaporates water from the slip. The spray-dried powder produced falls to the bottom of the dryer where it is unloaded by means of an extractor valve. Exhaust air goes through a set of cyclones to recycle the small quantity of fine powder it contains, then to a wet scrubber system for further cleansing before it is expelled as steam [4,6]. The two most important properties to be controlled are the moisture content and the size distribution of the granulate [4].
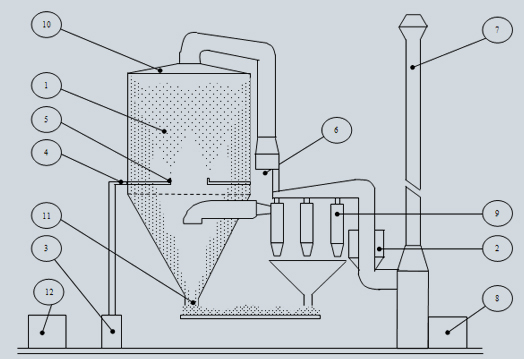
1 | Drying Tower | 7 | Chimney |
2 | Drier | 8 | Extractor Fan |
3 | Slip Pump | 9 | Fines Removing Cyclones |
4 | Lance | 10 | Warm Air Diffusor |
5 | Atomizing Nozzle | 11 | Extractor Valve |
6 | Warm Air Heater | 12 | Control Panel |
Figure 3. Diagram of Spray Dryer After Ryan [ 4] pg .122 |
The purpose of the pressing stage is to shape the spray dried powder into a compacted piece of unfired tile. Pressing is the simultaneous compaction and shaping of a powder or granular material confined in a rigid die or flexible mould [7]. Pressing of the spray dried granulate followed by drying determines the size and geometry of the product. The unfired strength is determined by the compaction achieved.
There are two types of presses namely the hydraulic press and friction press. The most commonly used presses in the ceramic tile industry are the hydraulic presses (Figure 4). They offer the advantage of a consistently high pressure which may be controlled relatively easily. They are preferably used in the manufacture of single-fired products such as, of glazed and unglazed vitrified stoneware tiles and of large-size tiles where a constant pressure is imperative for dimensional accuracy.

The pressing pressure differs for different types of tiles. In the case of white-body floor tiles, a pressure below 300MPa is used, while for vitrified tiles of the same size it is necessary to use pressures of 350-400MPa [1].
Drying of the ceramic tile is carried out between the pressing stage and the firing process. This is carried out to increase the strength of the unfired tile and also to reduce the risk of tile loss due to deformation as the tile rapidly shrinks or cracks as the steam is rapidly evolved in the kiln. The amount of water to be removed depends on the shaping method and it is about 3 to 6% for ceramic tiles. The drying of dust pressed tiles are safer than wares produced by the plastic shaping method with higher moisture contents because water that separates the particles in these latter wares are removed and causes a drying shrinkage. At present, tile body drying is performed automatically and continuously in vertical or horizontal fast dryers [4,8].
Firing is usually the final stage in the ceramic tile manufacturing, at which the weak, unfired, newly pressed piece of tile is transformed into a strong, durable product due to the effect of chemical and physical reactions within the green body during heating [9]. After firing, the ceramic tile body adopts the mechanical and aesthetic properties of the finished ceramic piece. Fast firing in a single layer ensures completely uniform temperature distribution and high quality of tiles as shown below.
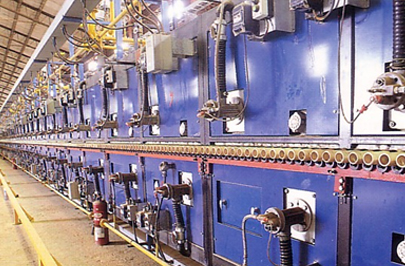
The goals of the firing process in rollers kilns(Figure 5) are mass vitrification and the dimensional stability in the firing temperature interval. A porcelain tile manufacturing plant ends with the sorting stage. In the selection line, planarity and quality of the pieces is of utmost priority [4].
- Biffi, G. "Fine Porcelain Stoneware Tiles - technology, production and marketing" Gruppo Editorale Faenza Editrice
S.p.A (1994) - Fugmann, K.G. "How to Produce Tiles-Preparation" Interbrick, Volume 5 No.3, pp.34-40(1989)
- Biffi, G.; Cini, L.; Pozzi, D.; Poppi, M. "Technical and Process Innovations in the Ceramic Industry" Ceramica Informacion, pp. 2-26 (September 1993)
- Ryan, W. "The Manufacture of Wall and Floor Tiles" Ceramic Research Company, Malaysia, pp. 52-75 pp. 99-147, pp.
185-200 (1999) - Fugmann, K.G. "Wet Way Continuous Milling in the Ceramic Tiles Industry" Interbrick, Volume 3 No.1, pp. 42-43 (1987)
- Smith, G. "Operating the Spray Dryer" Ceramic Industry, pp.54-56 (June 1993)
- Reed, J.S. "Introduction to the Principles of Ceramic Processing" John Wiley & Sons 1989
- SITI "Drying, Pressing" Societa Impianti Termoelettici Industriali CRC Centro Ricerche ceramiche Volume 5 La Tecnogia Ceramica, pp. 9-24, pp. 61-63
- Manfredini, T.; Pennisi, L. "Recent Innovations in Fast Firing process" Science of Whitewares, The American
Ceramic Society.